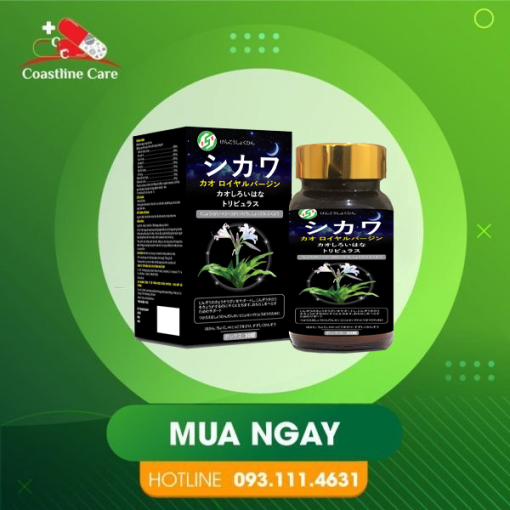
Branching out from the key problem, it is possible to make a approach map to check distinctive potential will cause. Utilizing a system map, it is possible to identify the gaps within your procedure which could produce your difficulty’s root cause.
Brainstorm probable causes: Stimulate workforce members to brainstorm all prospective will cause of the problem when producing the diagram. This could assist you in identifying all prospective root results in and ensuring that the alternatives are all-inclusive.
Utilizamos cookies para asegurar una mejor experiencia de usuario en nuestro sitio web. Si continúa utilizando este sitio asumiremos que está de acuerdo.Aceptar
Il est cependant doable de s’en servir pour développer l’entreprise, en indiquant un « fake effet » (un objectif à atteindre) et se servant des « 5 M » pour trouver des leviers plutôt que de pointer des brings about.
For effective brainstorming approaches when building an Ishikawa diagram, consider the following suggestions:
This type of tracking record can also be used to speak the workforce’s progress to management and buyers. New insights could possibly be acquired because the investigation progresses. For example, any individual checking the duration of a part could possibly have observed damage. This harm could then be entered into an up to date Ishikawa diagram after which transferred on the monitoring record.
To aid framework the approach, the types in many cases are picked from among the widespread products revealed below, but could arise as a thing unique to the application in a particular scenario.
Even with its simplicity, the Main framework stays regular: the key difficulty or problem statement occupies the fish’s head, while a few significant classes branch out from your central spine.
A producing business could have a dilemma with defects in finished items. An Ishikawa chart can nha thuoc tay help recognize doable leads to, for instance poor supplies, outdated machinery, human error from the creation approach, inconsistent Doing the job methods or top quality Management problems.
You need to use paper checklists nha thuoc tay or spreadsheets to define the issues or use unique instruments for instance SafetyCulture (previously iAuditor) to capture and organize your specified problems.
The advantages of working with Ishikawa Diagrams in these eventualities consist of improved top quality Regulate, minimized waste, enhanced employee retention and pleasure, and increased inventory management effectiveness.
Espinas secundarias. Son líneas que se desprenden de las espinas principales y que contienen las causas o los factores secundarios.
If the hypothesis just isn't supported, then another 1 within the prioritized monitoring record needs to be chosen and evaluated.
Being an Ishikawa tool and hazop application, SafetyCulture can make it nha thuoc tay straightforward to make and share checklists, assign duties, and keep track of the position of audits or investigations.